絡みやすいワークのばらし
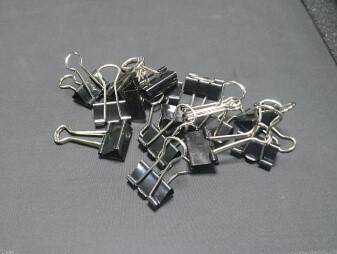
分離前
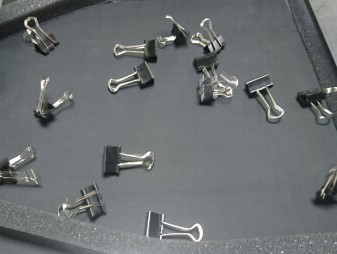
分離後
バラ積みピッキング 分離フィーダー
従来困難だった絡みやすいワークの分離や
狙った場所のワークの表裏反転を実現
ワークの姿勢・集積状態を画像認識し、ワークの載ったステージの傾動動作によるワークの移動と、移動打撃シリンダーによるステージ裏面から狙ったポイントの打撃により、従来はバラシが困難だったワークの確実な分離と、狙ったワークの表裏反転・姿勢変換を可能にしました。
アラインピッキングDFの特徴
絡みやすいワークや滑りにくいワークも分離可能
カメラ認識により、多品種混在ワークの仕分け可能
同一カメラで種類判別、表裏判定、分散状態を認識できる為、効率的
ワークの反転も可能(※ワークによる)
ワークを任意のエリアに移動させることも可能
ワーク専用パーツフィーダーにならない為、複数のワークに対して、1台のアラインピッキングで対応が可能
ワークをボウル内でかき混ぜるような動作が無い為、ワークへのダメージが少
最高60個/分の高速移載(スカラロボットタイプ)
ワークのトレイへの垂直挿入など自由度の高い後工程への移載が可能(6軸ロボットタイプ)
ワークの向きや位置を精度良く供給できるので、箱詰め、袋詰め、充填装置への供給など様々な用途に対応できます。
絡みやすいワークのばらし
分離前
分離後
表裏識別
表のワークを検出
表裏の反転
ポイント打撃前
ポイント打撃後
ワークを任意のエリアに移動
スカラロボットタイプ
60個/分の高速処理が可能
スカラロボットタイプ
60個/分の高速処理が可能
6軸ロボットタイプ
ワークのトレイへの垂直挿入など自由度の高い後工程への移載が可能
6軸ロボットタイプ
ワークのトレイへの垂直挿入など自由度の高い後工程への移載が可能
製品実績
電子部品コンデンサ
電子部品ブリッジダイオード
自動車部品パッドサポート
(金属異形部品)
アラインピッキングDF 動画紹介
アラインピッキングDF Ver2 動画紹介
アラインピッキングDF カタログ紹介
バラ積みワーク高速仕分けピッキング
当社従来方式より大幅な高速化を実現し、
ピッキング能力90ピック/分を達成しました。
従来当社のバイブレータを用いたバラ積みワークのピッキングシステムのスピードは、60ピック/分でした。
本システムは、バイブレータを用いたバラシエリアと、ロボットによるピッキングエリアを分離したことにより、ロボットの待機時間を減らし、処理能力を大幅に向上させました。
アラインピッキングHS-90の特徴
バラ積みワークからの90ピック/分の高速ピックが可能
ワークの画像を登録することにより、多種類のワークへの対応が可能
ワークの画像に基づき、混在ワークの識別、選別、仕分けが可能
カメラによりコンベア上のワーク量を認識して、ホッパーなどから自動でワークを供給
次工程に、ワークの向きや位置を精度良く供給できるので、箱詰め、袋詰め、充填装置への供給などが確実に行えます
アラインピッキングHS-90の用途例
●包装機、充填機、加工機へのワーク投入
●プレス機から排出されたワークの整列、箱詰め
●カゴ容器に入ったワークの次工程への投入
●ケース詰め・箱詰め、容器詰め
●複数種混在ワークの仕分け、選別
●表裏仕分け、方向整列
●製品検査の為の整列供給
アラインピッキングHS-90の対応ワーク例
サンプルワークをご提供頂ければ、当社テスト機にて検証を行い、最適な方法をご提案致します。
ばら積みワークからの高速ピック
ホッパーに入れたワークを切り出し、バイブレータにて平面分散。平面分散させるバラシエリアと、ピッキングエリアを分離し、90ピック/分の高速でのピッキングを可能にしました。
多品種対応可能、整列・排出パターンも自由自在
【樹脂個片(色識別)】
赤白混在したワークの色を識別し、指定したパターンで整列。
【チューブ(大小混在)】
大小混載するワークの大きさを識別し、大きさ別にキャップの方向を合わせて整列。
【金属個片(表裏判別)】
ロゴ印刷面が上面となっている個片のみをピックし、方向を合わせて整列。
アラインピッキングHS-90の装置構成
①供給コンベア
ホッパーや上流供給機構により投入されたワークを段階的に山崩しし、コンベア搬送します。
②平面整列機構
ベルトコンベア上で平面配列、ロボットピッキングを行います。
③2Dカメラ・照明
平面整列されたワークを画像処理により、ワークの位置・姿勢・種類を認識します。
④ロボット・ピックハンド
画像処理データに基づき、ワークのピックアップ及び指定場所、指定姿勢での移載をおこないます。ロボットは、高速動作及び省スペース設置が可能なスカラーロボットを使用します。
※本構成は代表例です。
アラインピッキングHS-90 動画紹介
アラインピッキングHS-90 カタログ紹介
取り出し工程からワークの箱詰め出荷工程まで対応
当社は既設のプレス機や成型機から出てくる部品のケース詰めの自動化において、プレス機や成型機の動作に同期してワークを取り出す取り出し工程からワークの箱詰め出荷工程まで対応しています。
高速プレス機アンローダー、部品ケース詰め(箱詰め)システムの特徴
既設高速プレス機や成型機に同期したNCアンローダーで部品取り出し工程から対応
コンベア上を流れてくるワークを、ロボットでピッキングし専用ケースに収納
ワークを画像認識する事で、ワークの方向整列や仕分けが可能
ケースとワークとのクリアランスが少ない場合でも、確実なケース挿入が可能
ワークピック部に、当社独自のフローティング機構を設ける事で、ワークのケース挿入時のダメージを軽減
ケース交換時にもピッキング作業を継続できるよう、高速でのケース交換が可能(ケース交換によるダウンタイム無し)
高速プレス機アンローダー、部品ケース詰め(箱詰め)システムの流れ
1. 部品取り出し
図 NCアンローダー(部品取り出し)
プレス機や成型機などからワークが連続して供給される場合に、プレス機や成型機の動作に同期したアンローダーで部品を取り出し、コンベアにワークが重ならないように供給します。
2. ピッキング
図 ピッキング部
そしてこのコンベアの上で、カメラによるワークの画像認識を行い、ワークの位置と向きなどを認識します。
コンベアの下流工程で、コンベアで移動しているワークの位置を推定し、ロボットでピッキングします(コンベア同期)。
3. 箱詰め
図 ワークのケースへの挿入(箱詰め)
ピッキングしたワークは、向きをそろえて、ケースに詰めます。
高速処理が必要な場合は、ロボットハンドの停止位置精度のばらつきが大きくなります。
ワークとケースの縁とのクリアランスが小さい場合は、ケースの縁との干渉を防ぎ、確実にケースに挿入するために、ワーク挿入ガイドを設けることができます。
4. 段積み・段バラシ
図 ケース段積み・段バラシ
ケースが満杯になると、空きケースと交換します。連続して、ワークをケースに挿入するためには、1回のピッキング動作時間内に、ケースの交換を完了させる必要があるため、ケースを高速で交換します。満杯になったケースは払い出され積み重ねられます。
ロボットを2台用いた掲載の装置の能力は最大120個/分です。
プレス機や成型機からのワークの処理についてお困りの場合はぜひご相談ください。
高速プレス機アンローダー、
部品ケース詰め(箱詰め)システム 動画紹介
高速仕分けピッキング装置を3台連結させたもので、より高速にワークを供給する必要がある場合に使われます。
かごや袋などの容器にばらばらの状態で供給されるバラ積みワークを、後工程に供給するための装置として様々な方法が提案されています。しかし、実際に自動供給装置がつかわれているのは一部にとどまり、多くの場合はまだ人手で供給されています。当社はこのような人手で供給されているバラ積みワークの自動供給方法の開発に取り組んでいます。
バラ積みワークの自動供給方法については以下のような方法があります。
これらの方法の中で、最も広く用いられているのは①のパーツフィーダー法ですが、適用できるワークは、ワークの外形基準で分離できるもの、表面が振動によるワーク同士のこすれによって傷つきにくいものなどに限定されます。また、できたとしても、装置ごとに対応できるのは1種類のワークだけのため、ワークごとに別の装置が必要で、なおかつワークによっては詰まりやすく工程が止まってしまうことがあるなど、使い勝手が悪いのが現状です。
③の3Dピッキング法は、3Dカメラでワークの外形を認識させれば、ワークが変わっても対応できます。しかし、データ処理及び、ロボットの姿勢を3次元的に位置制御してピッキングするために、1分間に十数個のピッキングが限界です(現状では最速でも5秒/個程度)。また、コスト的にも高いため、使われる用途は限定されています。
②の2Dピッキング法は、カメラでワークの違いが分かれば識別でき、多種類のワークに対応できるため、①のパーツフィーダー法に次いで多く使われています。しかし、ワークによっては、振動では平面に分散しにくいものも多く、また供給できる個数が数十個/分と人間の能力に比べれば少ないために、まだ汎用的には使われていないのが現状です。
当社では、このような現状に基づき、一般的な包装機などで求められる、1分間に100個以上の供給を目標に②の2Dピッキング法の改良に取り組んでいます。
1分間に100個の供給が可能な方法としては、コンベア上に1個ずつ完全に分離した状態で、2次元カメラでワークを撮影し、コンベアの進行速度を予測して、コンベアを止めずにコンベアの下流の予測した位置で、水平多関節ロボットによりピッキングする方法(コンベア同期法)が知られています。しかし、この方法は、バラ積み状態のワークに対しては、安定的に平面に分散させることが難しいためあまり使われていません。主として成型機の後工程など1個ずつ完全に分離して供給できる場合に使われています。ただし、移動中に動く可能性のある転がりやすいワークには使えません。
当社の高速ピッキングシステムでは、バラ積み状態のワークを入れたホッパーから、ワークに合わせた独自の方法でワークをコンベア上で平面に分散させ、2Dカメラで識別を行い、水平多関節ロボットでピッキングして、姿勢が悪くピッキングできないものは、コンベアで前工程に循環させて再度ピッキング工程に供給します。
この方法によると、振動フィーダー上でピッキングするよりも待機時間を少なくすることができるため、高速にピッキングすることができます。また、平面分散が完全でなくとも、トラブルになることは少なく、スピードにはあまり影響がないため安定的にピッキングすることができます。
当社における実績では、ワークとしてホテルなどの歯磨きセットに用いられる5cm程度の歯磨きチューブを用いた場合、従来の振動フィーダーを用いた方法では50個/分が限界でしたが、本方式を採用したところ90個/分程度と大幅に高速化する事ができました。
本方式では、混在しているワークでも別々にピッキングすることができます。このため混在ワークの仕分けにも用いることができます。